Wanneer je eens goed om je heen kijkt, zul je een heleboel kunststof producten zien. Veel van deze producten zijn gemaakt door middel van spuitgieten. Spuitgieten is namelijk een van de meest gebruikte vormgevingstechnieken voor kunststof onderdelen.
Wanneer je kunststof spuitgiet producten ontwerpt, heb je als ontwerper veel meer vrijheid in vormgeving. In vergelijking tot andere productieprocessen is kunststof spuitgieten een sneller productieproces.
In dit blogartikel staan wij stil bij kunststof spuitgieten. Wij leggen je uit wat het is en hoe het proces in zijn werk gaat. Dat doen we aan de hand van de volgende alinea’s:
- Productietechnieken voor kunststof
- Hoe werkt het spuitgietproces?
- Rekening houden met het proces
- Kunststof spuitgieten samen met Beeliners
Wil jij innoveren en jouw idee uit laten werken in samenwerking met Beeliners? Wij helpen je graag! Kom eens vrijblijvend langs voor een kopje koffie en we bespreken graag met jou de mogelijkheden.
Productietechnieken voor kunststof
Je kan kunststoffen op verschillende manieren bewerken. Denk bijvoorbeeld aan:
- Rotatiegieten
- Lasersnijden
- Draaien
- Frezen
- Spuitgieten
Kunststof halffabricaat bewerken door het te draaien en te frezen is een totaal andere techniek dan kunststofspuitgieten. Hier heb je vaak te maken met kleine oplages en zit je als ontwerper aan een vrij beperkte vormvrijheid in vergelijking tot kunststof spuitgieten. En heb je ook relatief veel materiaalverlies. Bij kunststof spuitgieten spreek je over grote aantallen een vrij korte tijd; massaproductie.
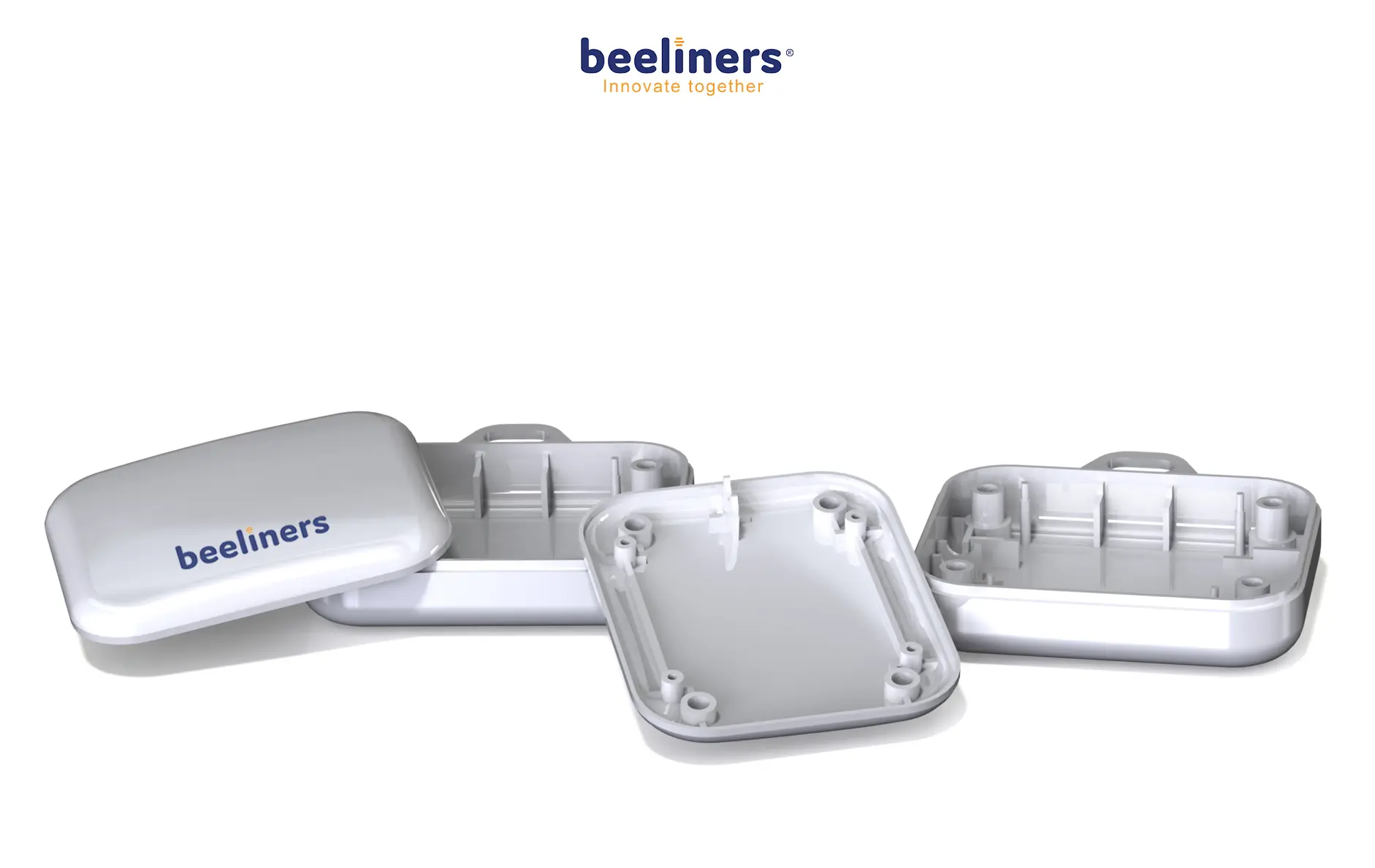
Hoe werkt het spuitgietproces?
Bij het spuitgieten worden kunststof korrels, beter bekend als granulaat, in een trechter gestopt waarna het via een verwarmde schroef met een hoge druk in een mal/matrijs wordt gedrukt. In een matrijs bevinden zich koelkanalen, schuiven en uitstootpennen (om een product uit de matrijs te drukken).
Omdat er veel verschillende kunststoffen zijn, met allen hun specifieke eigenschappen, heeft iedere soort kunststof zijn eigen uitwerking bij het spuitgieten. Om je kunststof product uit de matrijs te krijgen, dien je aan je ontwerp altijd “lossing” toe te passen, anders krijg je je product nooit uit de matrijs.
Wanneer je een kunststof product gaat spuitgieten spreek je ook over cyclustijden. Dit wordt bepaald door de tijd die de matrijs nodig heeft om te koelen. Wanneer je een vrij dikke wanddikte hebt, kan je begrijpen dat je meer tijd nodig hebt om te koelen, dan wanneer je een dunne wanddikte hebt.
Als je product te snel gekoeld wordt kan het er voor zorgen dat je product enorm gaat krimpen, met als resultaat dat je kunststof product zich gaat vervormen. Nou kan je dit probleem oplossen met koelen, maar een lange cyclustijd heeft effect op je kostprijs. En soms kan het helpen om een rib toe te voegen. Zoals je leest moet een ontwerper met heel veel dingen rekening houden, wanneer er gebruikgemaakt wordt van deze productie techniek.
Rekening houden met het proces
Als er tijdens je engineeringfase al rekening gehouden wordt met hoe je het product wil produceren en wat daar allemaal bij komt kijken, zit je al vrij gauw tegen een productierijp product aan. Het spel dat je uitvoert samen met de spuitgieter, zorgt er voor dat je goed moet kunnen communiceren maar ook je vormgeving moet waarborgen.
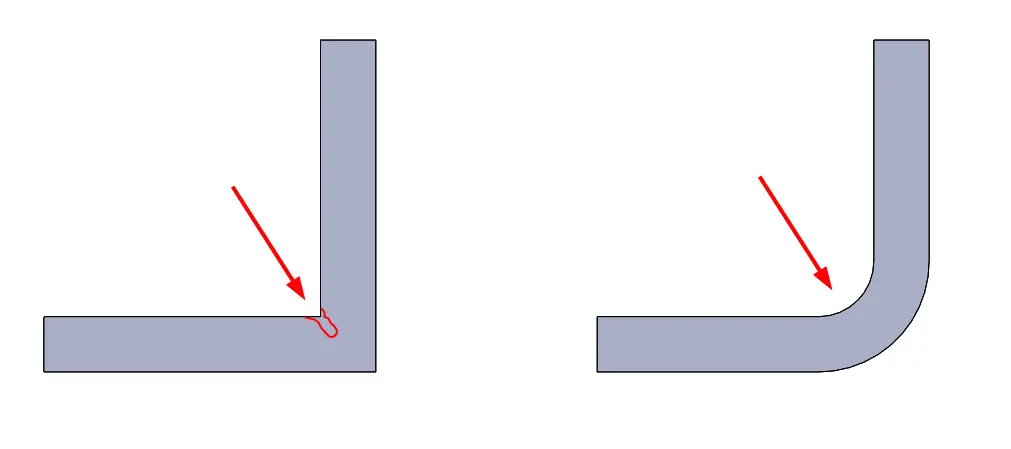
In bovenstaande afbeelding is te zien dat wanneer het ontwerp een constante wanddikte geeft (afbeelding rechts), het kunststof makkelijker in de matrijs gespoten kan worden. Houd je het haaks zoals links afgebeeld dan stroomt het kunststof niet goed de hoek om en ga je je in de hoek een vervorming krijgen.
Een andere veel voorkomende ontwerpfout zijn “sink marks” wanneer je een rib plaatst om bijvoorbeeld je oppervlakte te verstevigen maar deze geen radius geeft, kunnen er “sink marks” ontstaan. (zie onderstaande afbeelding links). Met een juiste wanddikte en hoogte van de rib en afrondingen kan je “sink marks” voorkomen.
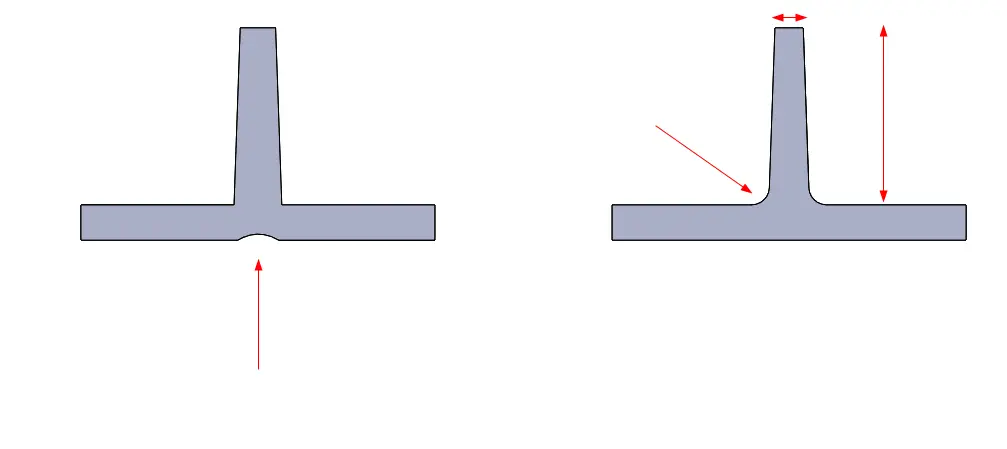
Zo zijn er een tal van zaken waar je rekening mee dient te houden wanneer je een kunststof product ontwerpt.
Kunststof spuitgieten samen met Beeliners
Binnen Beeliners helpen we bedrijven met innoveren. Daarbij ondersteunen we door snel tastbare prototypes te bouwen. Binnen dit soort ontwikkeltrajecten, waar je met verschillende disciplines samen werkt, moeten veranderingen snel worden doorgevoerd en in praktijk worden getest.
Het ontwikkelteam werkt veel in overleg. De processen zijn nauw met elkaar verbonden. Het team is de schakel van het prototype naar het productierijp brengen van een product. Vaak zorgen verandering in het ontwikkelproces dat een component gewijzigd moet worden, waardoor er dus meer ruimte binnen een behuizing nodig is. Daarnaast kan er hardware-matig zaken veranderen, waardoor je je design aan moet passen.
Dit proces is continu in ontwikkeling en zorgt er ook voor dat je je design moet bewaken voor soms grote wijzigingen. Wijzigingen die voor een hardware engineer niet groot zijn, kan voor mij een drastische verandering tot gevolg hebben. Hierbij kun je denken aan veranderingen in de vormgeving of dat een essentiële ondersteuningsrib aangepast moet worden. Ik vind het een kunst om samen tot een compromis te komen en elkaar continu uit te dagen. Daarmee komen we tot een resultaat waar we allemaal gelukkig van worden.
Binnen het ontwikkelproces is een belangrijke stap; het bevriezen van het ontwerp! Wanneer je een product bevroren hebt dan is dit een vast gegeven waar je naar kan refereren binnen het ontwikkelproces. Want je kan wel door gaan met het finetunen en uit engineeren van je product. Maar dan komt er nooit een product op de markt.
Behoefte aan ondersteuning op het gebied van innovatie en vernieuwing?
Zoals beschreven komt er veel kijken om een een prototype naar productiegereed product te krijgen. Een traject waarbij veel disciplines betrokken zijn en belangrijke afwegingen genomen moeten worden. Heb jij behoefte aan innovatie, ontwikkeltrajecten of ondersteuning bij het productiegereed maken van een concept, dan komen we graag met jou in contact. Neem contact met ons op voor een kennismakingsgesprek.